The impact of single-cell automatic spot welding machine with DC welding power supply on PACK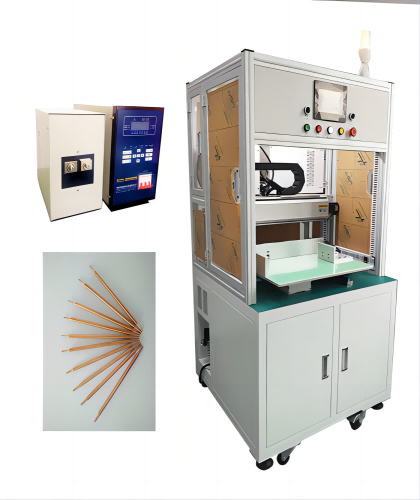
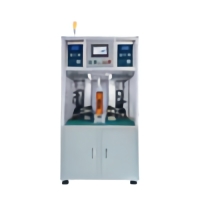
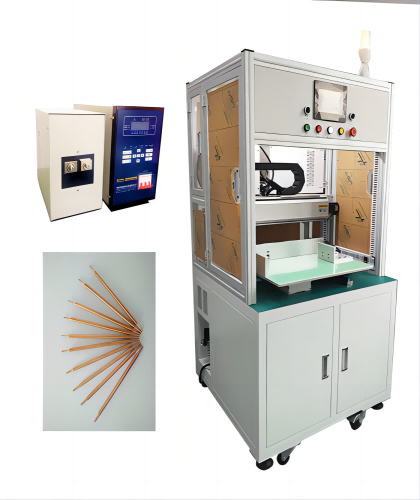
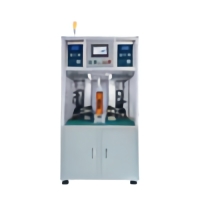
The single-cell automatic spot welding machine with DC welding power supply has many effects in the production of PACK (battery pack).
1. Positive impact
High welding quality:
The DC welding power supply can provide stable current output, ensure the heat stability during welding, and make the welds uniform and firm. This is crucial for battery connection in PACK. High-quality welding can reduce contact resistance, reduce energy loss, and improve the overall performance and efficiency of the battery pack.
Precise current control can avoid over-welding or under-welding, reduce welding defects, and improve the reliability and safety of PACK.
High degree of automation:
Single-cell automatic spot welding machine can realize automatic welding, improve production efficiency, and reduce errors and inconsistencies caused by manual operation. In PACK production, a large number of battery cells need to be connected. Automatic welding can ensure the stability of welding quality while reducing production costs.
Automatic spot welding machines are usually equipped with advanced control systems, which can realize accurate welding parameter setting and monitoring, and improve the controllability of the production process.
Adapt to different battery types:
The DC welding power supply can be adjusted according to different battery types and specifications to meet the welding requirements of various battery cells in PACK. Whether it is a cylindrical battery, a square battery or a soft pack battery, a good welding effect can be achieved through appropriate welding parameter settings.
For battery cells of different capacities and voltages, the single-cell automatic spot welding machine can also be flexibly adjusted to meet the diverse requirements of PACK design.
II. Potential risks and countermeasures
Thermal impact:
A certain amount of heat will be generated during the welding process. If the heat is not properly controlled, it may cause thermal damage to the battery cell, affecting the performance and life of the battery. In order to reduce the thermal impact, the welding parameters can be optimized, such as reducing the welding current, shortening the welding time, etc., and appropriate heat dissipation measures such as cooling systems or heat sinks can be adopted.
The batteries after welding are inspected and screened to promptly detect and eliminate battery cells that may have thermal damage to ensure the quality of PACK.
Electromagnetic interference:
The DC welding power supply may generate electromagnetic interference when working, which will affect the electronic components and control systems in the PACK. In order to reduce electromagnetic interference, shielding measures can be adopted, such as setting a shielding cover around the welding equipment, or considering electromagnetic compatibility in the PACK design.
Conduct electromagnetic compatibility testing on PACK to ensure that it is not affected by electromagnetic interference during welding.
Equipment maintenance and management:
Single-section automatic spot welding machines need regular maintenance and care to ensure their stable performance and welding quality. This includes cleaning the equipment, checking welding electrodes, adjusting welding parameters, etc. At the same time, the equipment needs to be calibrated and tested regularly to ensure that it meets production requirements.
Establish a complete equipment management system to standardize and record the use, maintenance and care of the equipment to improve the reliability and service life of the equipment.
In summary, DC welding power supply single-section automatic spot welding machines play an important role in PACK production. Through reasonable application and management, its advantages can be fully utilized to improve the welding quality and production efficiency of PACK, while reducing potential risks and ensuring the performance and safety of PACK.