Energy storage battery pack PACK production line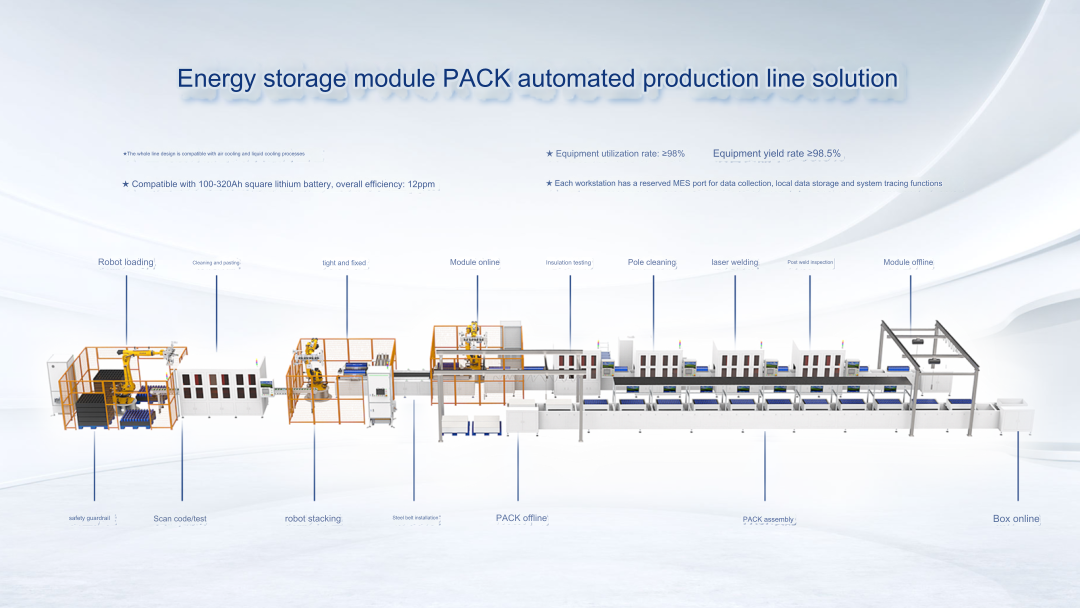
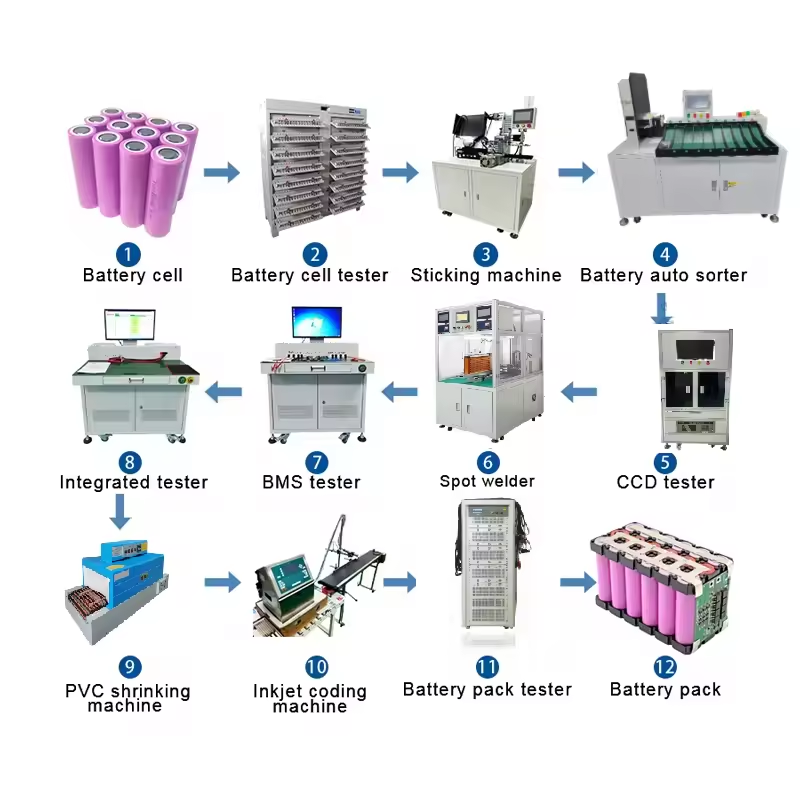
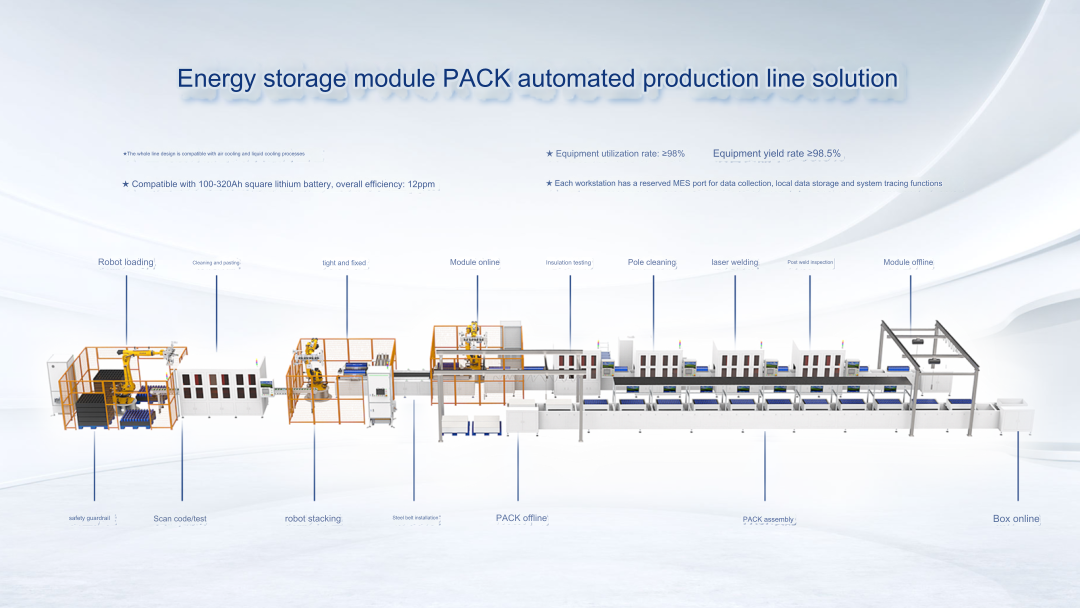
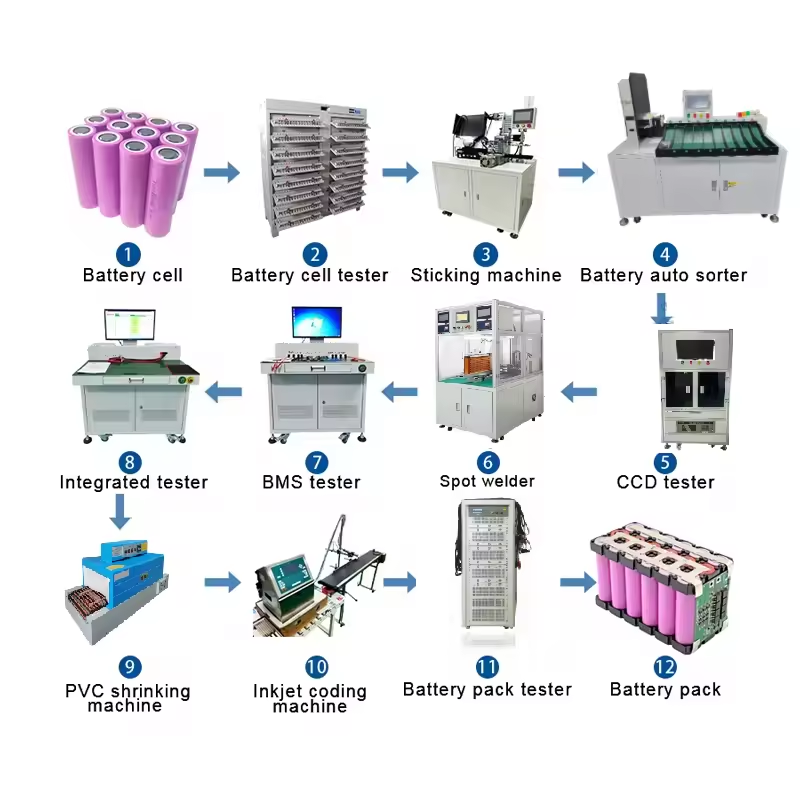
The energy storage battery pack PACK production line is a series of automated production processes for combining single lithium batteries into battery packs (PACK), which mainly includes the following parts:
Battery cell processing link:
Battery cell testing and sorting: This is the first step of the production line. The voltage, internal resistance, capacity and other parameters of the battery cell are strictly tested to select the battery cells that meet the standards and sort them according to performance parameters to ensure the consistency of the battery cells in each PACK. This link usually uses professional testing equipment, such as battery cell sorting machines, which can quickly and accurately detect and sort a large number of battery cells.
Battery cell stacking: The sorted battery cells will be transported to the stacking station and stacked together in a specific arrangement to form the basic structure of the battery module. In this process, the battery cells may be fixed with partitions and end plates, or the stability of the battery cells may be ensured by methods such as cable ties and extruded tooling steel strips.
Polarity detection and CCD addressing: Use visual positioning technology such as CCD system to detect the polarity of the battery cell and achieve high-precision addressing to ensure accurate alignment of each component and prepare for subsequent welding and other operations.
Welding link:
Bus welding: Weld the bus bar to the pole of the battery cell to achieve series and parallel connection of the battery cell. Welding quality is crucial to the performance of the battery, so advanced welding technologies such as laser welding, ultrasonic welding or pulse welding are usually used. Among them, laser welding has the advantages of high energy density, small welding deformation and small heat-affected zone, and is widely used.
Collection line welding: Used to weld the collection harness with other components to ensure the reliability of data collection. During the welding process, high-precision positioning systems and detection equipment are required to ensure the accuracy of the welding position and the reliability of the welding quality.
BMS integration and packaging link:
BMS integration: The battery management system (BMS) is a key component to ensure battery safety and efficiency. It will be integrated into each PACK to monitor and manage battery voltage, current, temperature and other parameters to protect and control the battery.
Packaging: The shell is packaged to protect the battery from external influences, and it also plays the role of insulation and protection. The selection of packaging methods and materials needs to be determined according to the specific application scenarios and customer needs.
Testing stage:
Semi-finished product testing: At each stage of the PACK assembly process, corresponding tests will be carried out, such as post-welding inspection, including inspection of welding quality, electrical performance testing, etc., to ensure the product quality of each link.
Finished product testing: The assembled energy storage battery pack PACK is subjected to comprehensive performance testing, including charge and discharge testing, cycle life testing, safety performance testing, etc., to ensure that the final product meets relevant standards and customer requirements.
Packaging stage: The qualified battery packs are packaged for transportation and storage. The packaging materials and methods need to have good protective performance to protect the battery packs from damage during transportation and storage.
In addition, the energy storage battery pack PACK production line also includes logistics conveying systems and control systems, which are used to realize automatic material transportation, coordinated control of the production process, and data management and monitoring. The design and layout of the entire production line need to fully consider factors such as production efficiency, product quality, safety and maintainability to meet the needs of different customers.