Semi-automatic production line for cylindrical battery packs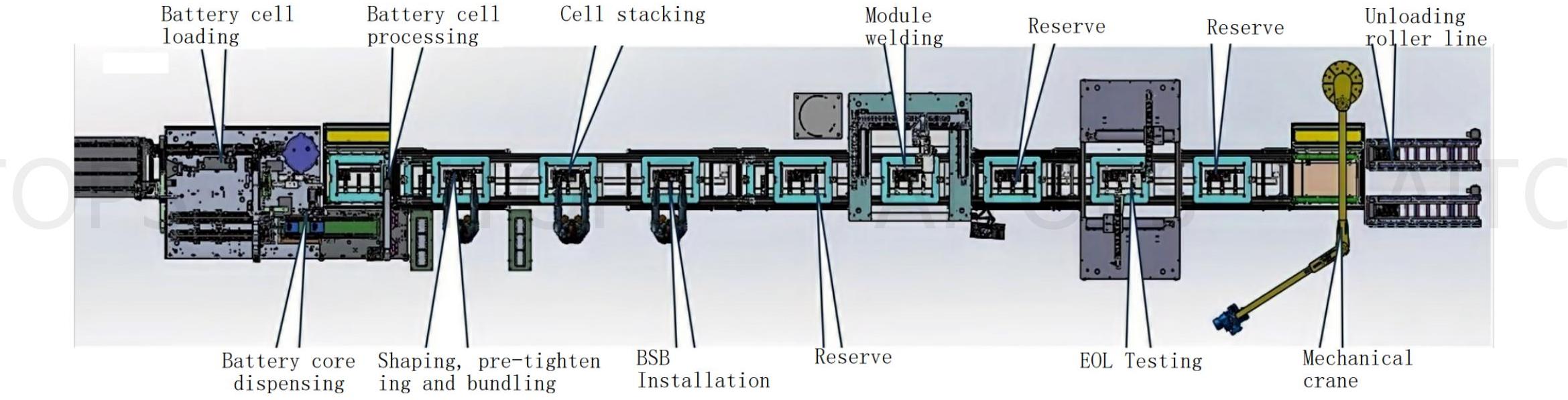
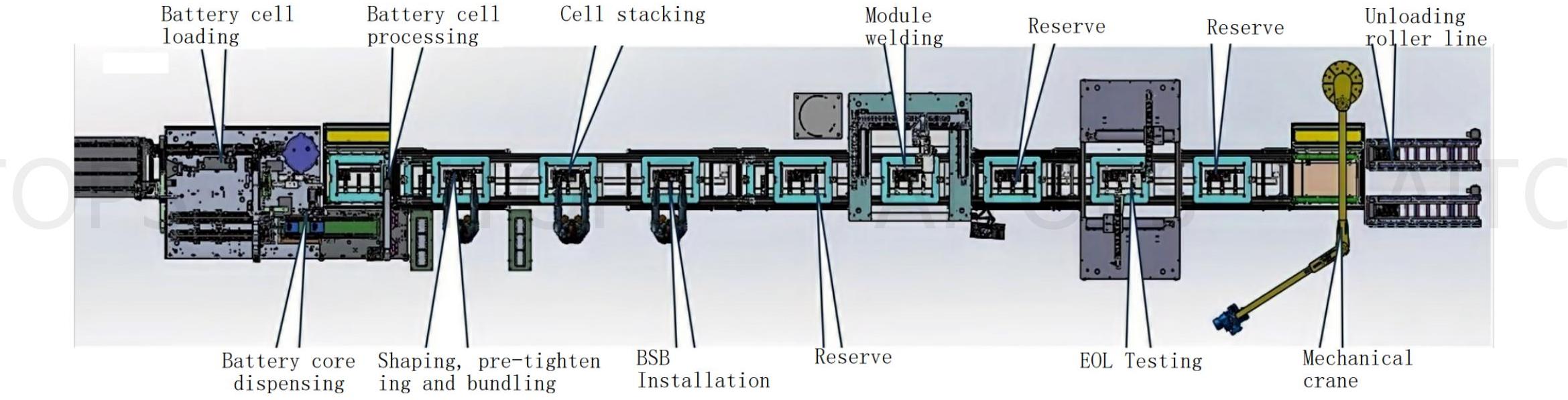
The semi-automatic production line for battery packs is a production method in which some processes use automated equipment and some processes still require manual intervention during the production of battery packs. The following is a detailed introduction to the relevant situation:
I. Components
1. Automated process equipment
-Battery cell feeding equipment: responsible for automatically conveying the battery cells to the designated position on the production line in the set order and method to ensure the continuity and accuracy of the battery cell supply, such as the grabbing and transfer of the battery cells through conveyor belts, robotic arms, etc.
Welding equipment: For the connection of battery packs, such as series and parallel welding between battery cells, automatic laser welding machines or ultrasonic welding machines will be used. These devices can accurately control the welding parameters, ensure the consistency and stability of the welding quality, and realize the reliable connection between the battery cell tabs.
Detection equipment: including automatic internal resistance detection instruments, voltage detection equipment, etc. They can quickly and accurately detect the various performance indicators of the battery pack during the production process, and timely screen out unqualified products, such as whether the internal resistance of the battery cell exceeds the standard and whether the voltage is within the qualified range.
2. Manual intervention process and supporting equipment
Battery cell sorting and pairing: Although there are some automatic detection equipment to assist, manual work still needs to further sort and accurately pair the battery cells according to the test results to ensure that the battery cells that make up the battery pack are as matched as possible in terms of performance (such as capacity, internal resistance, etc.) to improve the overall performance of the battery pack. Usually equipped with simple auxiliary tools, such as label guns for marking battery cell performance parameters.
Some operations in the battery pack assembly process: For example, in the process of installing the battery cell into the battery pack shell, it may be necessary to manually place the battery cell in place and connect some auxiliary components (such as temperature sensors, etc.). At this time, some manual tools such as screwdrivers and tweezers will be used.
Appearance inspection and repair: Manual inspection of the appearance of the completed battery pack to check whether there are scratches and whether the shell is tightly installed. If small defects are found, manual repair tools (such as sandpaper to polish small bumps, glue to stick small parts, etc.) may be needed to repair them.
2. Advantages
1. Cost advantage: Compared with fully automatic production lines, semi-automatic production lines have relatively low equipment procurement costs. Because there is no need to configure a full set of highly automated equipment, for some small and medium-sized enterprises, the capital investment pressure is relatively small, and it is easier to achieve the start of large-scale production of battery packs.
2. High flexibility: Semi-automatic production lines are easier to modify when switching products or adjusting production processes. Since some processes rely on manual operation, unlike fully automatic production lines, which are highly dependent on procedures and equipment, they can adapt to the production needs or process improvement requirements of different types of battery packs relatively quickly.
3. Convenient for quality control: There are many links in the production process where humans participate, and they can more intuitively find some problems that may be missed by automated equipment, such as minor damage to the surface of the battery cell and abnormal appearance of the welding part. Through manual secondary inspection and intervention, product quality can be better guaranteed.
III. Disadvantages
1. Relatively low production efficiency: Since some processes require manual operation, the speed and accuracy of manual operation are limited after all, and cannot be compared with the efficient and fast operation of fully automated equipment, so the overall production efficiency will be lower than that of fully automatic production lines, and it is difficult to meet large-scale and ultra-high-speed production needs.
2. High dependence on manual labor: There are many links in the production process where humans participate, which means that there is a high dependence on manual labor. If there is a shortage of labor or manual operation errors, it may lead to problems such as obstruction of production progress and unstable product quality.
3. Poor product consistency: Although there are automated equipment to ensure the quality of some processes, manual operation may introduce some differences in human factors. For example, different workers have different operating methods and proficiency, which may cause the battery pack to be slightly less consistent in performance and appearance than the products produced by the fully automatic production line.
IV. Application scenarios
1. Small and medium-sized production enterprises: These enterprises have relatively limited funds and cannot afford the high cost of fully automatic production lines, but they need to produce battery packs on a certain scale. Semi-automatic production lines can help them gradually develop their business and meet some of the market's demand for battery packs while controlling costs.
2. New product development and small-batch production: During the development stage of new battery pack products, product design and production processes may not be stable and need to be adjusted frequently. The flexibility of semi-automatic production lines makes them very suitable for small-batch production in the development process of new products, so as to obtain product feedback in a timely manner and optimize products and processes.
3. Customized battery pack production: When facing customers' customized needs, such as battery pack production with specific performance requirements and special appearance design, semi-automatic production lines can better realize these customized contents through manual intervention to meet customers' personalized needs.
Battery pack semi-automatic production lines have a unique position and role in the field of battery pack production. Enterprises can consider whether to choose this production method based on their actual situation, such as financial strength, production scale, product demand, etc.