Power battery pneumatic spot welder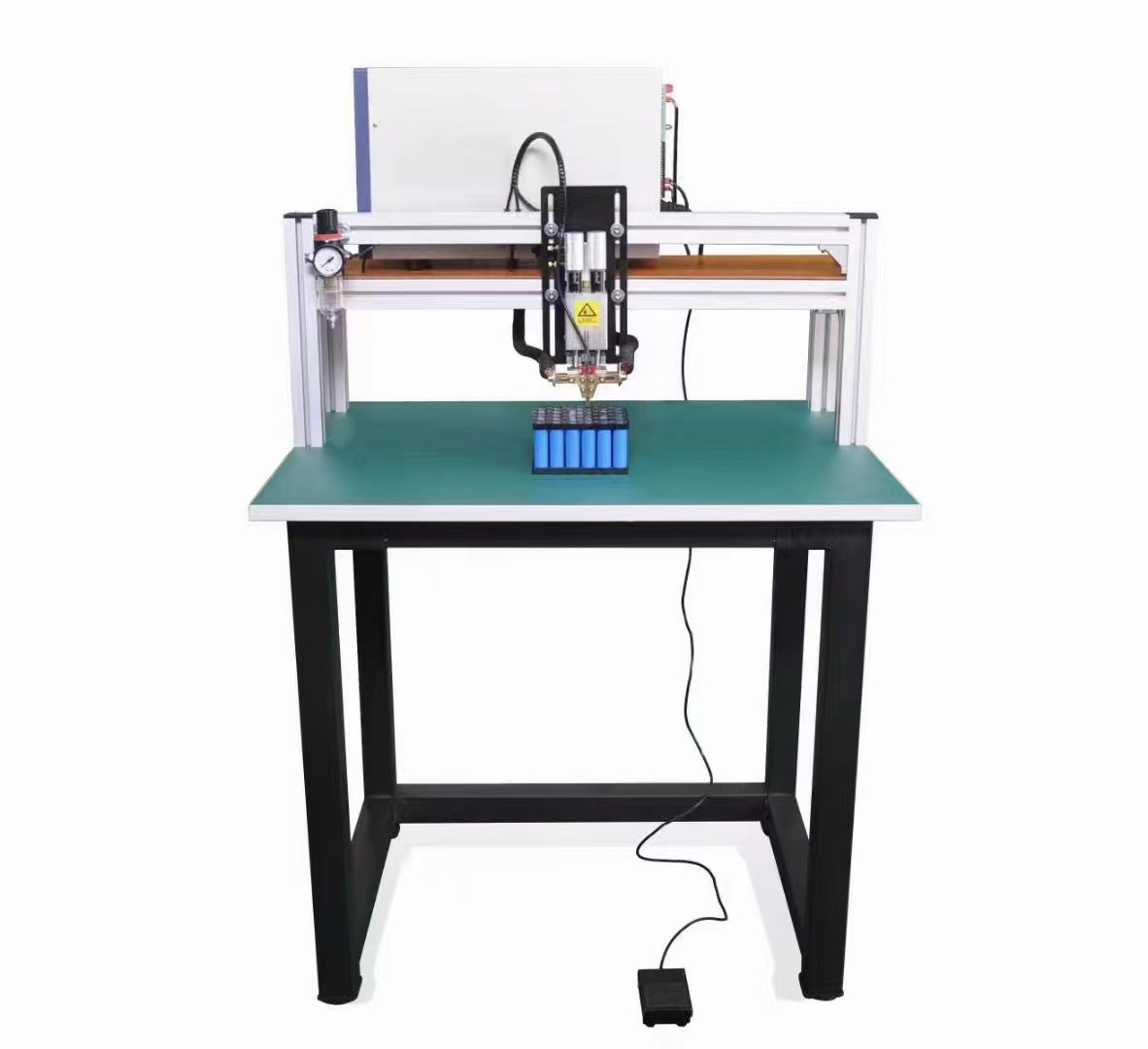
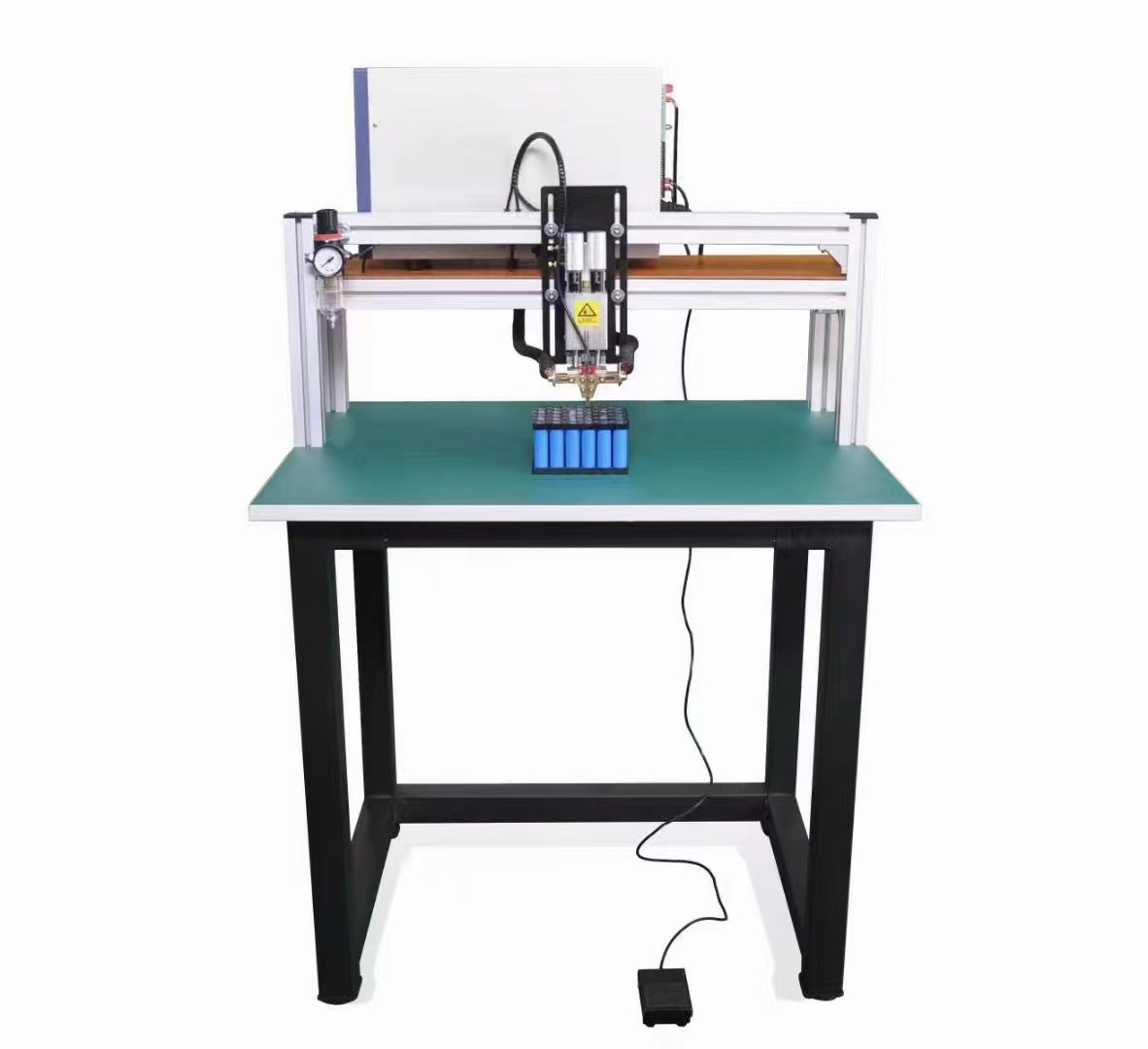
Power battery pneumatic spot welder is a kind of equipment specially used for welding battery tabs and other parts in the production and manufacturing process of power batteries. The following is a detailed introduction for you:
1. Working principle
It mainly works based on the principle of resistance welding. When the current passes through the workpiece to be welded (such as battery tabs and connecting pieces), resistance heat will be generated at the contact part, causing the metal at the contact point to quickly heat up to the melting point and fuse together, thereby achieving welding. The pneumatic part provides pressure for the welding electrode to ensure close contact between the workpieces during welding to ensure good electrical conduction and heat transfer conditions, making the welding more firm and reliable.
2. Structural composition
Welding transformer: responsible for reducing the voltage of the input AC power to provide low voltage and high current output suitable for welding. This is a key component for generating the heat required for welding.
Pneumatic system: usually includes cylinders, solenoid valves, gas source processors, etc. The cylinder is used to drive the up and down movement of the welding electrode to provide welding pressure; the solenoid valve controls the air intake and exhaust of the cylinder to achieve precise control of the electrode movement; the gas source processor purifies and regulates the input compressed air to ensure stable operation of the pneumatic system.
Electrode: It is in direct contact with the workpiece to be welded and is the key part for transmitting current and pressure. Electrode materials are generally selected from metals with good conductivity, high temperature resistance and wear resistance, such as copper alloys, and their shapes and sizes are designed according to the specific requirements of the welding workpiece.
Control system: Welding parameters such as welding current, welding time, and electrode pressure can be accurately set and controlled. Some advanced control systems also have functions such as data recording and fault diagnosis, which facilitate the management of the production process and equipment maintenance.
III. Features
High welding quality: It can achieve precise control of welding parameters such as current, time, pressure, etc., so as to ensure the consistency and reliability of the welding point, which is crucial to ensure the electrical performance and safety of power batteries.
High efficiency: The pneumatically driven electrode moves quickly, and the welding process is relatively short. A large amount of welding work can be completed in a short time to meet the needs of mass production of power batteries.
Adapt to a variety of materials: It can effectively weld metal materials such as copper, aluminum and their alloys commonly used in power batteries, and by adjusting the welding parameters, it can adapt to the welding of workpieces of different thicknesses and specifications.
Convenient operation: It is generally equipped with an intuitive human-machine interface, and the operator can easily set and adjust the welding parameters, and can operate the equipment proficiently after simple training.
4. Application fields
It is mainly used in the production and manufacturing of various types of power batteries, including but not limited to lithium-ion batteries, nickel-hydrogen batteries, etc. In the battery assembly process, it is used to weld the positive and negative ears of the battery with the connecting pieces, busbars and other components. It is an indispensable and important equipment for building battery modules and battery packs.
5. Technology development trend
Intelligence: The future power battery pneumatic spot welding machine will be more intelligent, with adaptive welding parameter adjustment function, which can automatically optimize welding parameters according to the real-time conditions such as the material and thickness of the welded workpiece, and improve welding quality and efficiency.
High precision: With the continuous improvement of the performance and safety requirements of power batteries, the requirements for the welding accuracy of spot welding machines are also getting higher and higher, including the precise control of welding positions and the consistency of welding point sizes.
Energy saving and environmental protection: While meeting the welding needs, by optimizing the transformer design, using energy-saving pneumatic components and other measures, the energy consumption of the equipment is reduced and the impact on the environment is reduced.