Advantages of battery pack PACK automated production line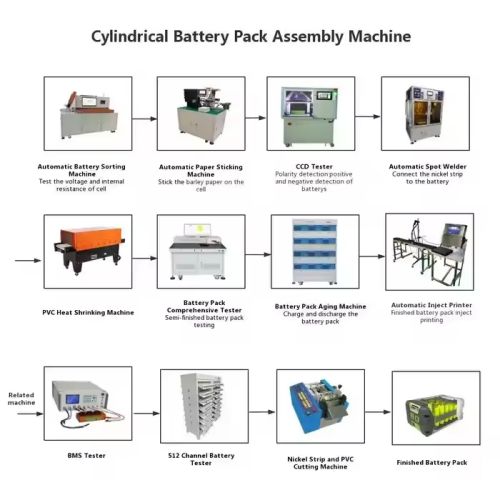
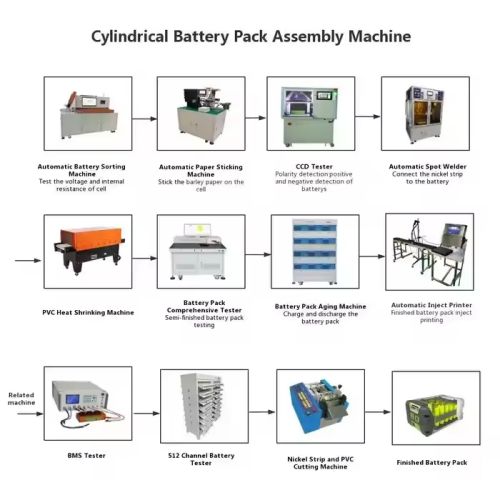
Battery pack PACK automated production line has many advantages, as follows:
Improve production efficiency:
High-speed operation: Automated equipment can run uninterruptedly, and compared with manual assembly, it can complete more battery pack PACK production tasks per unit time.
Process optimization: Automated production line can closely connect various production links, reduce waiting time and material handling time between processes, and make the entire production process smoother and more efficient. For example, through automated conveying devices, battery components that have completed the previous process can be quickly transported to the next process, avoiding time waste during manual handling.
Improve product quality:
High-precision operation: Automated equipment uses advanced sensors, control systems and mechanical structures to achieve high-precision production operations.
Strict quality inspection: The automated production line is equipped with online inspection equipment, which can perform real-time inspection of battery packs during the production process, and promptly detect and eliminate unqualified products.
Reducing human errors: Manual operations are easily affected by factors such as fatigue and emotions, resulting in errors in the production process. The automated production line can avoid the impact of human factors on production quality and improve product stability and consistency.
Reduce production costs:
Reduce manpower requirements: Automated production lines can replace a large number of manual operations, reduce the company's demand for labor, and thus reduce labor costs.
Improve material utilization: Automated equipment can accurately control the amount of materials used in the production process, reducing material waste.
Reduce equipment maintenance costs: The equipment of automated production lines usually has high reliability and stability, long maintenance cycles, and relatively low maintenance costs. Moreover, the maintenance of automated equipment can be carried out through intelligent monitoring systems for predictive maintenance, to detect potential problems of equipment in advance and reduce the occurrence of equipment failures.
Enhance production flexibility and adaptability:
Quickly switch production modes: Automated production lines can quickly switch to produce battery packs of different models and specifications through programming and adjustment of equipment parameters to meet the diverse needs of the market. For example, when an enterprise needs to produce a new model of battery pack, it only needs to enter the corresponding production parameters in the control system, and the production line can automatically adjust the production mode to achieve rapid switching.
Easy to achieve customized production: For some customers with special needs, automated production lines can be customized according to customer requirements and provide personalized product services.
Improve production safety:
Reduce safety accidents: Automated production lines can free workers from some dangerous production links, reducing the risk of safety accidents caused by workers' exposure to high temperature, high pressure, toxic and hazardous substances, etc.
With safety monitoring function: The automated production line is equipped with a complete safety monitoring system, which can monitor the safety status of the production process in real time. Once an abnormal situation is found, it can promptly alarm and take corresponding safety measures to ensure the safety of production.