Working principle of fully automatic OCV test and sorting machine for cylindrical batteries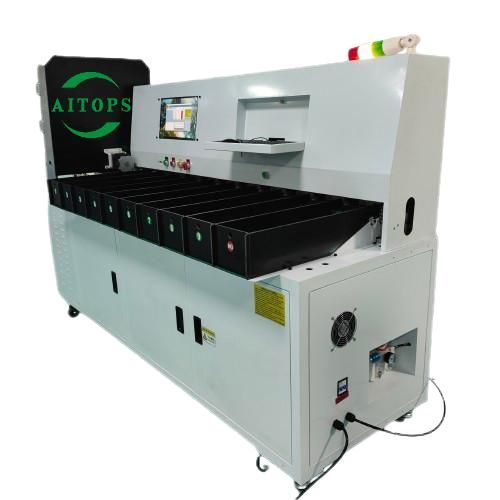
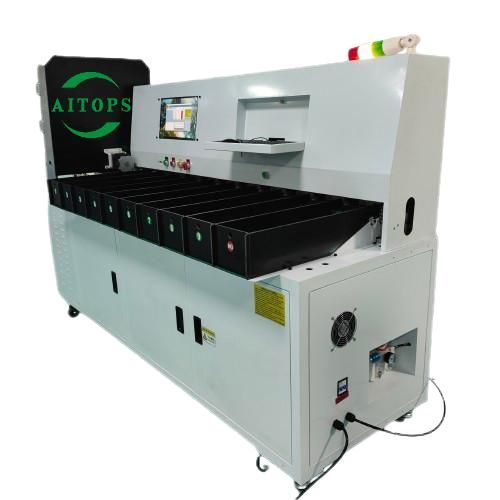
The working principle of fully automatic OCV test and sorting machine for cylindrical batteries mainly includes the following steps:
Loading stage:
Manual or mechanical device places the cylindrical battery to be tested into the loading area of the sorting machine. The common loading mechanism discharge bin is made of bakelite with a special loading box. The motor drives the rolling groove teeth to roll the batteries into the battery conveyor to the cache material belt in sequence, completing the preliminary loading operation and preparing for subsequent testing.
Feeding stage:
The battery is conveyed to the test area by a feeding device such as a PVC belt. The discharge method is usually one out of two, that is, the conveyor belts on both sides are conveyed and tested respectively, which can be carried out synchronously, greatly improving the test efficiency.
Testing stage:
Contact and measurement: When the battery is conveyed to the test position, the electrode or probe of the test device contacts the positive and negative poles of the battery to form a test circuit. The high-precision voltage measuring instrument begins to read the open circuit voltage (OCV) value of the battery. During this process, the test system will keep the battery in an open circuit state to accurately measure its open circuit voltage.
Data transmission: The measured OCV value is transmitted to the central control system in real time. The control system is usually composed of a high-performance processor and related circuits, which can quickly receive, process and store data.
Sorting stage:
Comparative judgment: The central control system judges the measured battery OCV value according to the preset voltage range and sorting criteria. For example, batteries with OCV values within a certain range are classified into the same grade or category.
Sorting operation: Based on the judgment result, the control system will issue instructions to the sorting device, such as a manipulator, a cylinder clamp mechanism, etc. The sorting device accurately places the battery in the corresponding sorting channel or gear. For example, if it is a 10-gear sorting machine, there will be 10 different sorting channels, corresponding to different OCV ranges.
Discharging stage:
The sorted batteries will be transported along their respective sorting belt lines for subsequent packaging, storage or further processing.
The entire process is fully automated, reducing manual intervention, improving test efficiency and accuracy, and being able to quickly and accurately perform OCV testing and sorting on a large number of cylindrical batteries, ensuring that only batteries that meet quality requirements enter the next process or are shipped out of the factory.