What is battery module EOL detection?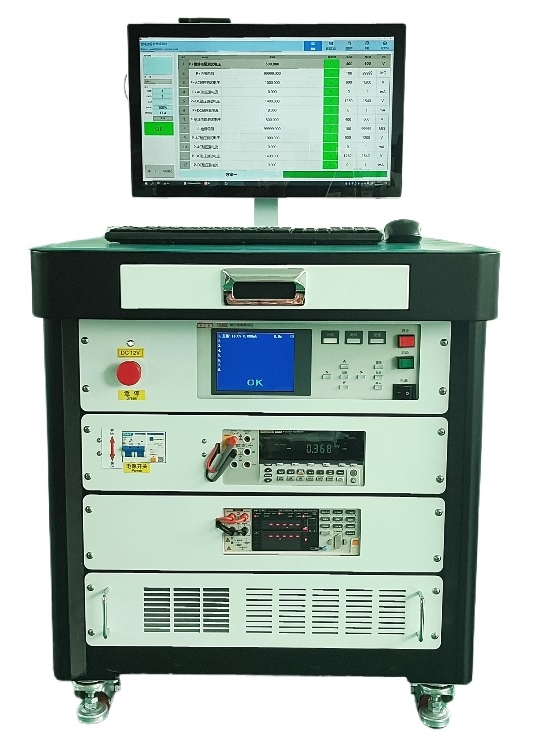
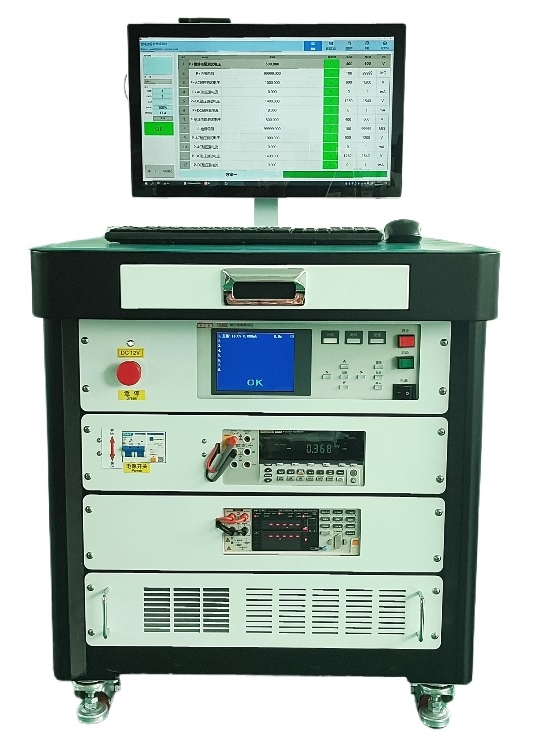
Definition
Battery module EOL (End-of-Line) detection refers to a series of comprehensive tests performed when the battery module is off the production line. Its purpose is to ensure that the quality and performance of the battery module meet the design requirements and can be safely and reliably applied to actual products such as electric vehicles, energy storage systems, etc.
Test content
Electrical performance test
Capacity test: measure the actual available capacity of the battery module through charge and discharge cycles. For example, for a battery module with a nominal capacity of 100Ah, under specific charge and discharge conditions (such as charge and discharge current, temperature, etc.), detect whether the actual amount of electricity that can be discharged is close to 100Ah. This is a key indicator for measuring the ability of the battery module to store electrical energy.
Internal resistance test: The internal resistance of the battery module affects its charge and discharge efficiency and power output. A professional internal resistance tester is used to measure the AC impedance between the positive and negative electrodes of the battery module at a certain frequency. Generally speaking, the smaller the internal resistance, the smaller the energy loss of the battery module during the charge and discharge process. For example, for power lithium battery modules, lower internal resistance can reduce the heating phenomenon during high-rate discharge.
Open circuit voltage detection: When the battery module is in an open circuit state (i.e., there is no external current path), measure the voltage between its positive and negative electrodes. The open circuit voltage can reflect the state of charge (SOC) of the battery module, and different SOCs correspond to different open circuit voltage ranges. The power status of the battery module can be preliminarily judged by open circuit voltage detection.
Safety performance detection
Insulation performance test: It mainly checks the insulation resistance between the positive and negative electrodes of the battery module and the module shell. Use an insulation resistance tester to apply a certain DC voltage (such as 500V or 1000V) and measure the insulation resistance value. If the insulation resistance is too low, it may cause leakage of the battery module and cause a safety accident. For example, in electric vehicles, poor insulation performance of the battery module may cause electric shock to passengers.
Overcharge and over-discharge protection test: By simulating the extreme conditions of the battery module during charging and discharging, detect whether its protection circuit is working properly. In the overcharge test, the charging voltage is increased to exceed the normal charging cut-off voltage to observe whether the protection circuit can cut off the charging current in time; in the over-discharge test, the battery module is discharged to a voltage lower than the normal discharge cut-off voltage to check whether the protection circuit can stop discharging, so as to prevent the battery module from being damaged due to overcharging or over-discharging, or even serious safety problems such as thermal runaway.
Mechanical performance testing
Dimension and appearance inspection: Use measuring tools (such as calipers, micrometers, etc.) to check whether the dimensions of the battery module meet the requirements of the design drawings. At the same time, check whether the appearance of the battery module has defects such as scratches, bumps, and deformation. For example, during the assembly of the battery module, if the outer shell is squeezed and deformed, it may affect the arrangement and connection of the internal batteries, thereby affecting the performance and safety of the battery module.
Vibration test: Simulate the vibration environment that the battery module may encounter during actual use, such as bumps during car driving. Fix the battery module on the vibration table and perform vibration tests according to a certain vibration frequency, amplitude and time. The vibration test can detect whether the internal connection of the battery module is firm and whether the battery will be displaced. For example, if the solder joints inside the battery module become loose under long-term vibration, it may cause poor contact, increase internal resistance, and even cause faults such as circuit breakage.
Testing equipment and technology
Professional testing equipment: such as high-precision charge and discharge testers, internal resistance testers, insulation resistance testers, vibration test benches, etc. These devices can accurately simulate various working conditions and accurately measure various performance indicators of battery modules.
Automated testing technology: With the continuous expansion of battery production scale, automated EOL detection systems are becoming more and more popular. Through automated testing, detection efficiency can be improved and human errors can be reduced. For example, an automated charge and discharge detection system can automatically complete the charge and discharge process of the battery module according to a preset program, and record and analyze data in real time.
Importance
For battery module manufacturers, EOL testing is a key link in ensuring product quality. Through strict testing, unqualified products can be prevented from entering the market, the after-sales failure rate of products can be reduced, and the reputation and competitiveness of the company can be improved. For end users, battery modules that have undergone EOL testing can provide safer and more stable performance and extend the service life of the product. For example, in the electric vehicle industry, reliable battery module EOL detection can ensure the vehicle's driving safety and the stability of its cruising range.