How to choose welding equipment suitable for lithium battery pack welding?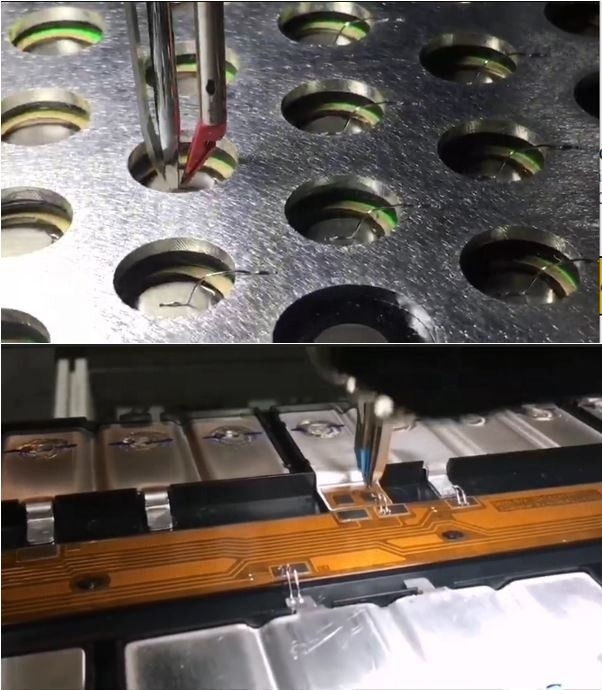
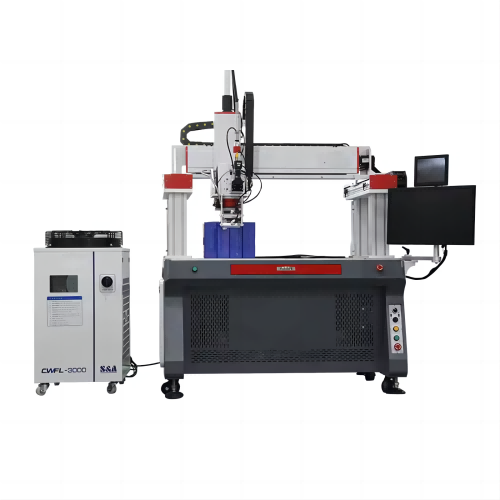
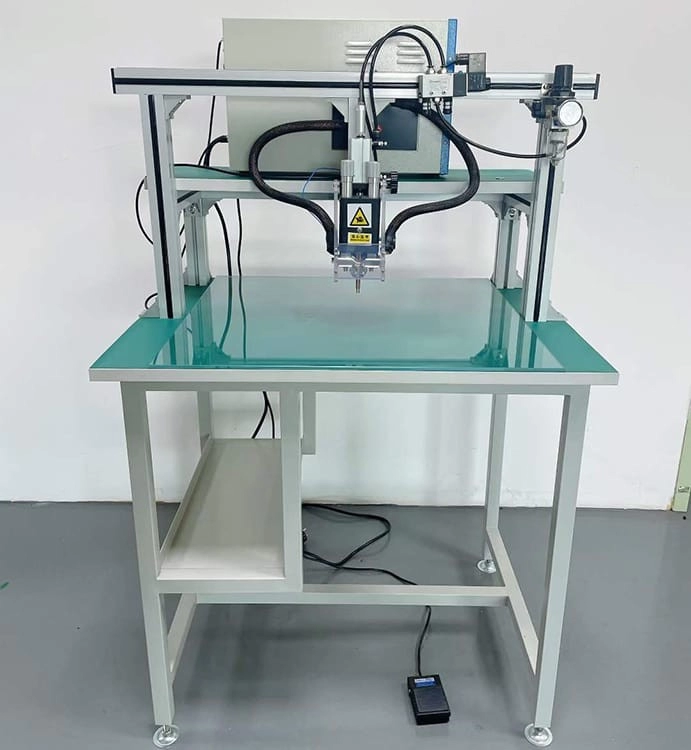
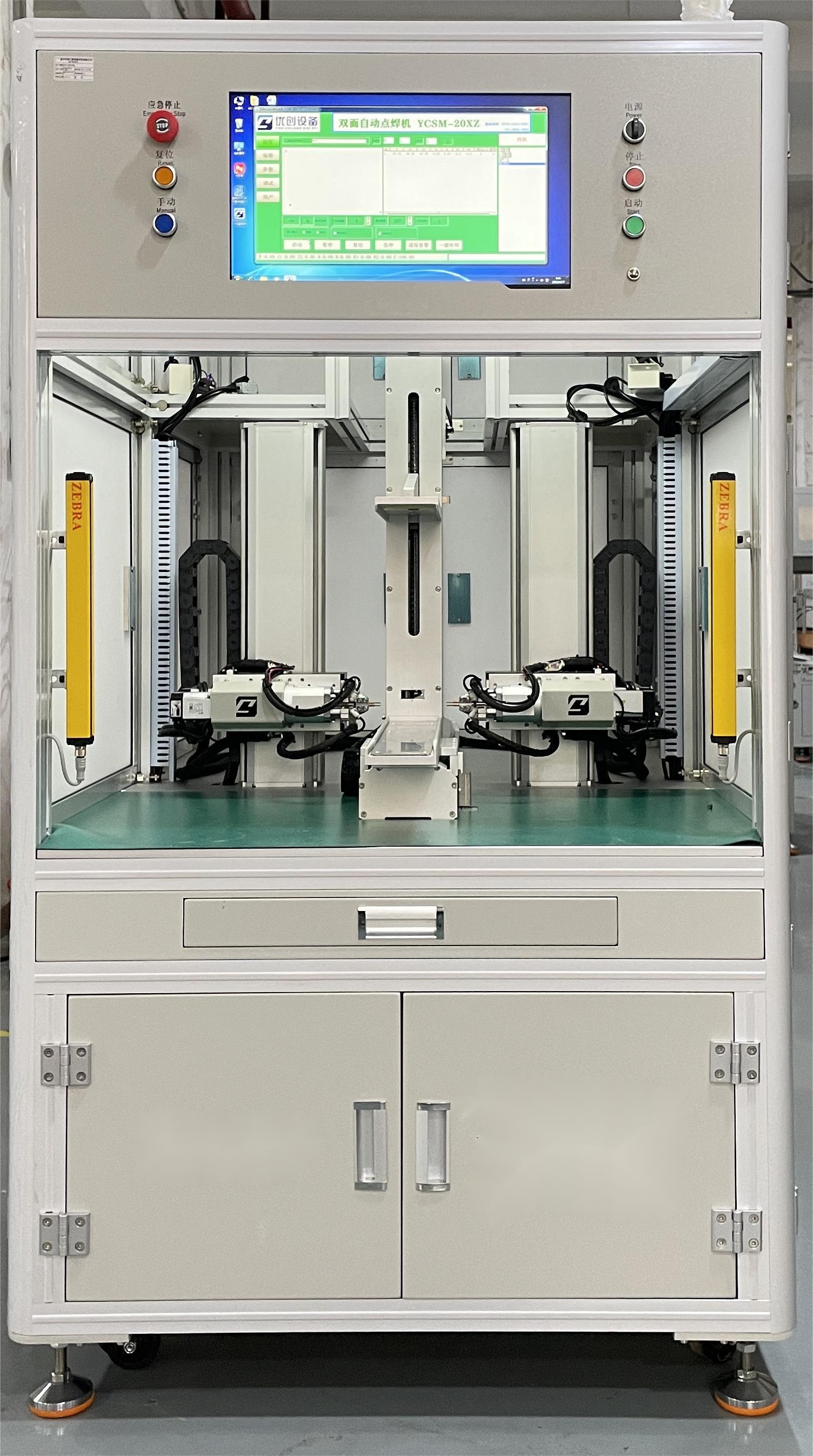
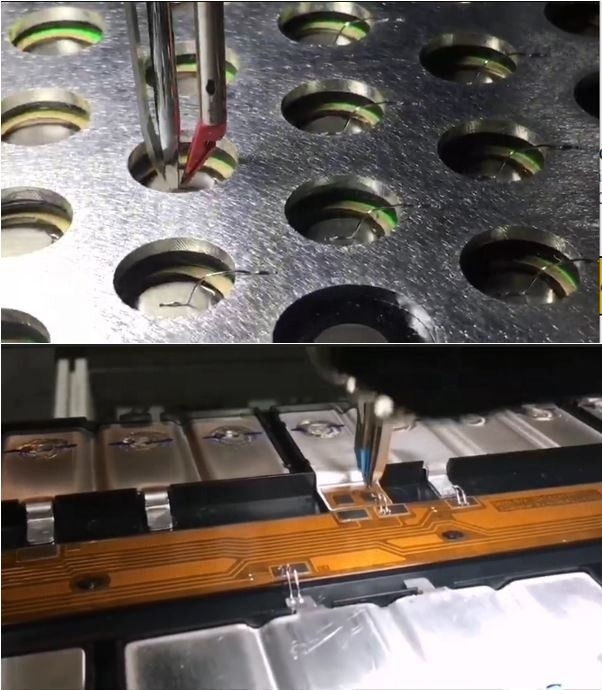
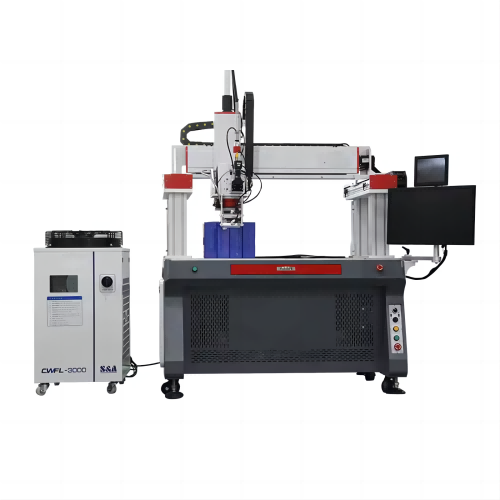
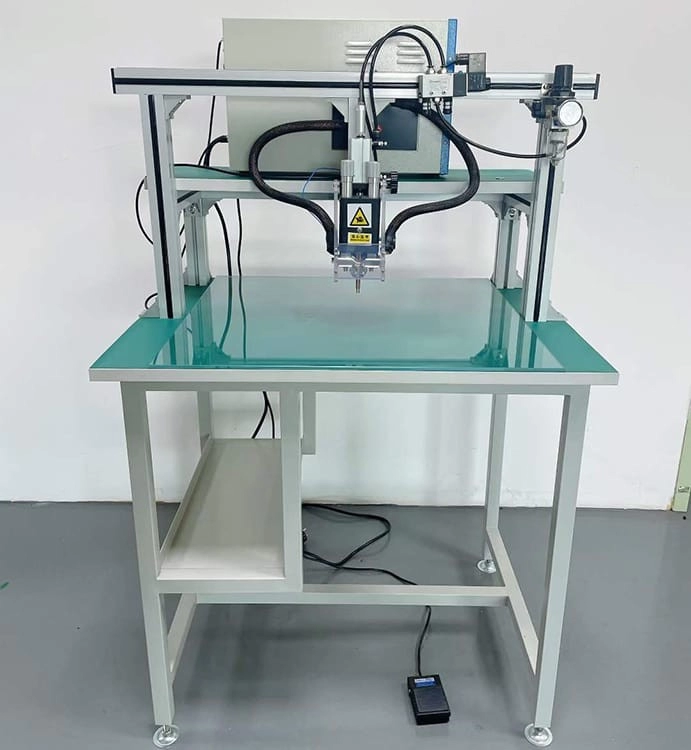
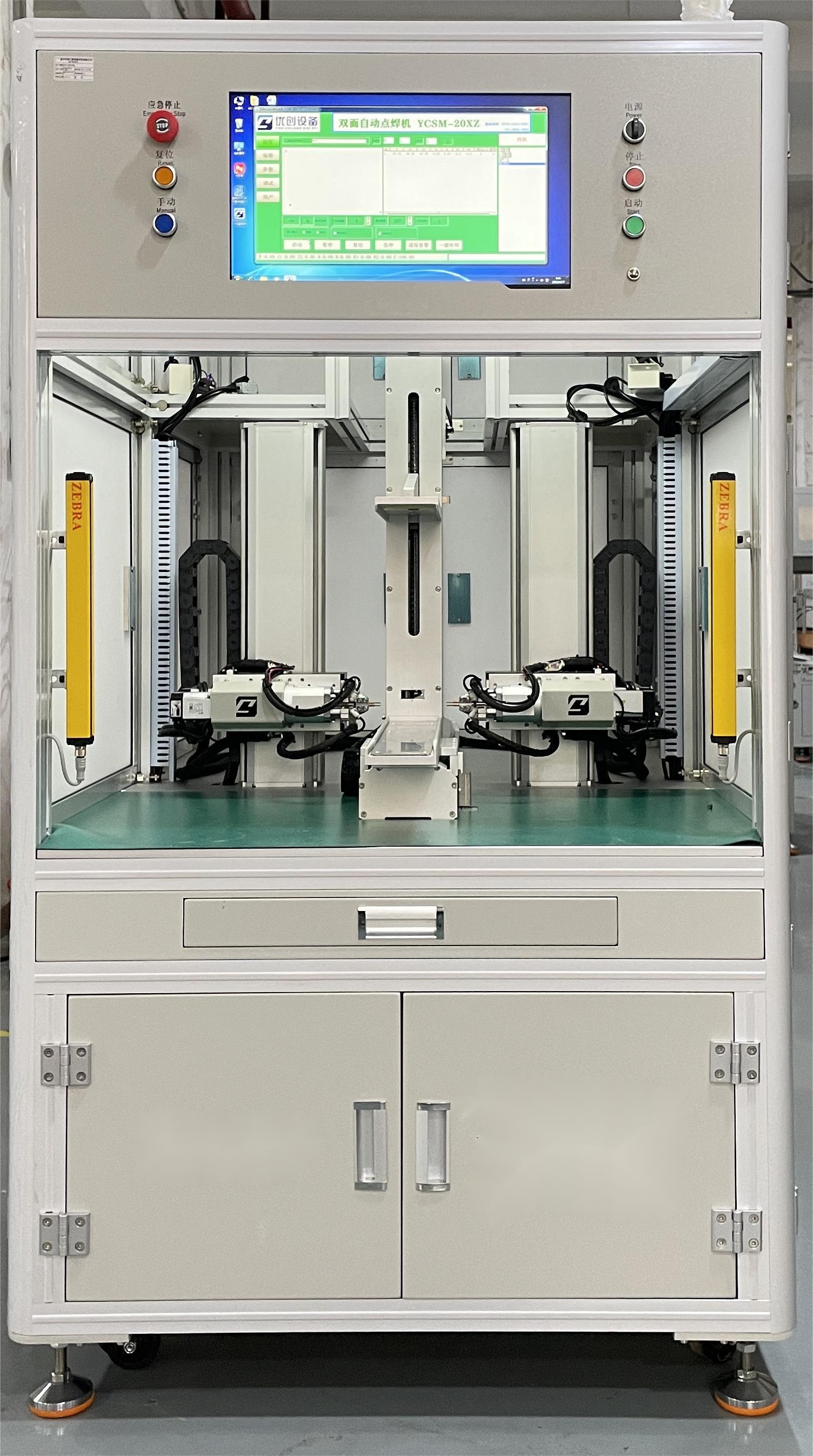
The following aspects need to be considered when choosing welding equipment suitable for lithium battery pack welding:
1. Applicability of welding method
Resistance spot welding:
Advantages: fast welding speed, high efficiency, small heat-affected zone during welding, and less damage to lithium batteries. Suitable for welding thin plates and small structural parts.
Considerations: It is necessary to select appropriate welding current, welding time and electrode pressure to ensure welding quality. At the same time, pay attention to the shape and size of the electrode to adapt to different welding parts.
Laser welding:
Advantages: high welding accuracy, extremely small heat-affected zone, can achieve welding of complex shapes, and high welding strength.
Considerations: Laser welding equipment is expensive and requires professional operators. In addition, laser welding has high requirements on the surface quality of welding materials, and it is necessary to ensure that the surface of the lithium battery pack is clean and flat.
Ultrasonic welding:
Advantages: No external heat source is required during welding, and the thermal effect on lithium batteries is small. Suitable for welding components such as plastic shells and metal terminals.
Considerations: It is necessary to select appropriate ultrasonic welding parameters, such as frequency, amplitude and welding time. At the same time, attention should be paid to the design of the welding joint to ensure the welding strength.
2. Equipment performance parameters
Welding current and voltage:
According to the material and thickness of the lithium battery pack, select the appropriate welding current and voltage range. Excessive current and voltage may cause the lithium battery to overheat, damage or explode, while too small current and voltage may not achieve good welding results.
Welding time and frequency:
Welding time and frequency should be adjusted according to welding materials and process requirements. Too long welding time may cause lithium batteries to overheat, while too high welding frequency may damage the internal structure of lithium batteries.
Precision and stability:
Choose welding equipment with high precision and stability to ensure the consistency of welding quality. High-precision equipment can achieve more accurate welding position and size control, while equipment with good stability can reduce fluctuations and errors during welding.
3. Safety performance
Protective measures:
Welding equipment should have good protective measures, such as protective covers, protective glasses, etc., to prevent sparks, spatters and radiation during welding from causing harm to operators.
Electrical safety:
Ensure that the electrical system of the welding equipment is safe and reliable, with functions such as overload protection, short circuit protection and leakage protection. At the same time, pay attention to the good grounding of the equipment to prevent electrical accidents.
Lithium battery safety:
Choose equipment specially designed for lithium battery pack welding. These equipment usually have special safety features, such as overvoltage protection, overcurrent protection and temperature monitoring, to prevent accidents during the welding process.
4. Brand and after-sales service
Brand reputation:
Choose welding equipment from well-known brands. These brands usually have high quality and reliability and provide good after-sales service. You can learn about the reputation of different brands by consulting product reviews, consulting industry experts or referring to the experience of other users.
After-sales service:
Ensure that the welding equipment supplier provides complete after-sales service, including equipment installation, commissioning, training and maintenance. Good after-sales service can ensure the normal operation of the equipment and reduce production interruptions caused by equipment failure.
In short, the selection of welding equipment suitable for lithium battery pack electric welding requires comprehensive consideration of factors such as the applicability of the welding method, equipment performance parameters, safety performance, brand and after-sales service. In the selection process, you should evaluate and compare according to your actual needs and choose the welding equipment that best suits you.